Last steel seam on Wendelstein 7-X closed
Core of fusion device completed / difficult installation stage successfully terminated
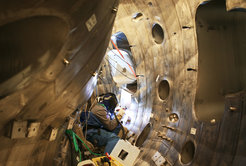
The objective of fusion research is to derive energy from fusion of atomic nuclei, just as happens in the sun. To ignite the fusion fire, the hydrogen plasma fuel in a future power plant has to be confined in magnetic fields and heated to temperatures exceeding 100 million degrees. Wendelstein 7-X, the world’s largest fusion device of the stellarator type when completed, is intended to investigate the suitability of this configuration for a power plant. With 70 large superconducting magnet coils in continuous operation it is then to produce a highly stable and thermally insulating magnetic cage confining the plasma.
The ring-shaped device is being installed as five almost structurally identical modules: Each of the five sections of the plasma vessel, along which 14 magnet coils are strung, is enclosed by a steel outer sheath, weighing altogether 120 tons. Assembled like slices of cake on the machine’s foundation, the five modules form a steel ring from which numerous connection ports protrude. These link the apertures of the plasma chamber through the coil region with the outer vessel. Later, measuring instruments, pumps and heating facilities will be affixed here.
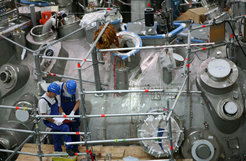
The 254th and last port was brazed in between the plasma vessel and outer vessel with millimetre precision on 28 May 2013. The elaborate port installation lasted a good two years. This was preceded by an equally long test phase – “a huge training session” as installation head Dr. Lutz Wegener put it – during which the methods for exact placement and connection of the variously configured ports to the bizarrely shaped plasma vessel were developed. One of the many challenges: As stainless steel inevitably shrinks at the seam when it is brazed, the components are distorted and change position. This had also to be allowed for when brazing the five modules of the device together: Calculations and tests during installation planning had predicted here up to eight millimetres shift per seam, this being intolerable since the ports and the subsequently connected measuring instruments would be looking at the wrong place in the plasma.
The solution: The module to be brazed, exactly monitored by laser tracker measurements, was shifted on sliding bearings about eight millimetres away from its firmly attached component opposite. Then, to prevent anything shifting, several welders began together to close the two brazing gaps of both the plasma chamber and the outer sheath. For the multi-layered seams with a total length of 40 metres the specialists of the MAN Diesel Turbo company took several weeks, during which the heavy module – in keeping with the shrinkage – slowly returned to its initial position in tenths of a millimetre steps. “It is a veritable work of art to guide in the right direction such a big and heavy component during brazing”, states Karsten Liesenberg, who is responsible for the vessel installation concept: “If the laser trackers showed that the module was not being shifted exactly parallel, the brazing crew had to change over to the opposite side of the seam so that the component was again put on the right track”. This precision work was repeated on the other four module boundaries. The ring is meanwhile closed and all five modules are in place with the required two millimetre precision.
Till installation of Wendelstein 7-X is completed in 2014, there are still a few tasks to be done, such as linking the magnets to their power and helium supplies and doing the interior of the plasma vessel. This will be accompanied by provision of the systems for heating the plasma, the supply facilities for electric power and cooling, machine control and finally the numerous measuring instruments for diagnosing the behaviour of the plasma.
Isabella Milch