An alternative for the energy supply of ASDEX Upgrade
If the flywheel generator EZ2 at the Max Planck Institute for Plasma Physics (IPP) in Garching were to fail, no replacement would be available. Supercapacitors could be a solution.
Here, electrical engineer Antonio Magnanimo describes a new concept for generating electricity for the IPP tokamak ASDEX Upgrade using supercapacitors. He developed this as part of his doctoral thesis at IPP which he finished in June. In the meantime, Dr Magnanimo has taken up a position at MIT in the USA.
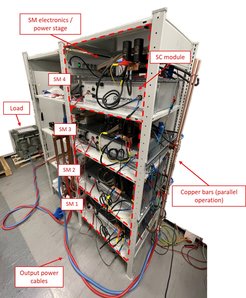
The electrical power of the tokamak experiment ASDEX Upgrade at the Max Planck Institute for Plasma Physics (IPP) in Garching is provided by three independent flywheel generators. They are charged up before the start of each experiment with up to 15 megawatts for several minutes. The stored energy is then used to satisfy the high-power needs during an experiment - called plasma pulse - of up to 450 megawatts. The three flywheel generators have been built only for this experiment more than 30 years ago. The largest one, EZ2 (built in 1973), could not be replaced in case of a major fault. Since the flywheel generators market has changed in the last decades, there exist no present company able to produce nowadays a flywheel generator with this size. Therefore, the development of an alternative power supply system with high power and energy and fully controllable output is planned.
The first idea consisted in conducting a feasibility study on the adoption of several smaller flywheel generators in parallel to reach the same power required by EZ2, but the outcome of this research was not successful due to synchronization issues. Since modern flywheel generators seem to be not an option, IPP decided to search for a different technology with similar energy and power density. Common batteries have higher energy density but too low power density, leading to a huge excess of (unused) energy in order to reach the required power; capacitors on the other hand have a very high power density, but a low energy density leading to an extreme expensive and large solution. For these reasons it has been decided to investigate on the upcoming technology of supercapacitors, which fits with flywheel generators in terms of both energy and power density. In order to deliver the required power to ASDEX Upgrade coils however supercapacitors are not enough, and a proper power converter is necessary taking into account a suitable safety concept.
How the idea for a modular system came about.
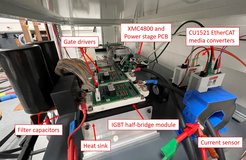
There exist already some supercapacitors-based power supplies for fusion applications, but all those systems use supercapacitors in a most simple configuration, meaning as a single passive bank integrated into a single powerful converter controlling the full energy flux. This would be the equivalent supercapacitor-based solution of a flywheel generator which would solve the current problem of replacing EZ2, but on the other hand it would present its main concern: supercapacitors are sensitive against overvoltage and they cause an electric short circuit in case of a failure. If this happens, the energy of thousands of parallel or serial connected cells could be injected into the faulty cell which is equivalent to a huge explosion. Loss of the full device and millions of Euro investment would be the consequence. This concern led to the search of a modular system and from here the idea of combining together supercapacitors with the modular multilevel converter was born: this converter has several identical small-scale power converter modules (submodules) that can control individually small scale supercapacitor modules; in this way in case of failure of a single supercapacitor module or submodule, the whole converter would not be affected or it could even continue the operation with a proper fault management. Right now there exists no similar solution as the one described in my dissertation on the free market, and for this reason it has been decided to keep the design as much flexible as possible, so that in case of need it can be adapted for different tokamak loads (poloidal field coils, heating systems…) or even non-fusion applications (e.g. electrical grid stability).
Working principle of supercapacitors
Supercapacitors are well known for their balanced ratio of energy and power density. Thanks to their high power density, supercapacitors have several potential applications, but they are mainly used for Uninterruptible Power Systems (UPS) and Hybrid Electric Vehicles (HEV). However, this technology does not provide enough energy for use in purely electric cars without being combined with a battery system.
Fundamentally a supercapacitor consists of two metal plates separated by an insulator, just like an ordinary capacitor. The separator, however, is porous and is soaked in an electrolyte. Since the ions of the electrolyte can move freely through the separator, positive and negative ions move in opposite directions and cling to their respective electrodes. The electrolyte acts as an (ion) conductor. The important feature in supercapacitors is that the inner surface of each electrode is not a smooth surface but it is rather padded with activated (porous) carbon. This results in a surface area that is up to 100.000 times as large as the surface area of an ordinary capacitor. The large surface area of a supercapacitor, however, is not the only novel feature of the device. Since charges are carried by ions attached to the inner surfaces of the electrodes these cannot be neutralised by electrons up to voltages of a few volts, the distance between the positive and negative charges at each electrode is on the order of a few Angstrom (one Angstrom corresponds approximately to the typical distance between atoms in a crystal compound and is the ten-millionth part of a millimetre). By maximizing the surface area and minimizing this distance, supercapacitors achieve extremely high values of capacitance (thousands of Farad for each cell). If the distance between the electrodes would be a millimeter, the electrode area of a single cell would have to be of the size of Germany. Because it is only one Angstrom, the area size is equal to approximately 30 soccer fields.

The use of supercapacitors for higher voltages is possible only by making use of supercapacitors modules, composed by several cells connected in serial. However, it is usually necessary to introduce active or passive components to balance evenly the modules internal voltages, thus increasing the global costs and complexity. In order to mitigate these inconveniences, manufacturers provide assembled modules reaching hundreds of Volts and Farad.
Applications of supercapacitors in fusion research.
One of the first fusion applications where supercapacitors have been used is PROTO- SPHERA in Italy, a “Spherical Tokamak” with the scientific goal to get rid of the central transformer. Another example is the Divertor Tokamak Test (DTT) facility, currently under construction in Italy. DTT is a large fusion experiment expected to provide relevant contributions to ITER and DEMO by investigating the problem of the power exhaust. DTT has six modules composing the central solenoid and six poloidal magnets, all superconductive and supplied by independent circuits via supercapacitors.
The power supply systems at PROTO- SPHERA and at DTT are both designed in such a way that in case of a major failure, the entire supercapacitor system would be damaged - analogous to the failure of a flywheel at ASDEX Upgrade. A solution that could replace a flywheel generator at IPP has to be capable to continue the operation even in case of local small faults, due to the importance of the experiments conducted and the much higher involved stored energy.
My concept for ASDEX upgrade is based on a modular multilevel converter (MMC). The MMC has received considerable attention since the beginning of this century and it has become one of the most attractive converters for high-power applications such as High-Voltage DC (HVDC) converters or railway power supplies, but also fusion devices’ power supplies. This converter, thanks to the discrete-leveled output voltage and its identical submodules by which it is composed, represents a promising alternative to replace the flywheel generator EZ2. The modular concept separates the total stored energy into thousands of smaller storages which can be kept separated even in case of fault.
As part of my dissertation, I built a small-scale demonstrator (1:550) to validate the designed converter. It is composed by four identical submodules, which can be connected in serial, parallel or combined serial/parallel connection. The aim of the demonstrator was to verify the results of the simulations I had previously carried out with the PLECS software tool. The supercapacitor module is a custom solution built for this specific project from the SPSCAP company. The module is composed of 48 supercapacitor cells in series, each of which has a capacitance of 3200 F and 2.7 V of nominal voltage. The module has no active electronics in it and it is treated as a passive single component, even though it presents a passive balancing system for its internal cells.
After having properly designed and tested the single submodule, three additional submodules have been built in order to test them in serial, parallel and combined serial/parallel operation. The serial operation was used to test the developed control strategy, the parallel was crucial for the scalability of the system and their combination validated the integration of both aspects into a single device.
A system for ASDEX upgrade would have to consist of 2200 submodules
All tests confirmed the results of the simulations. Therefore, the developed model can be used as a reference to scale the prototype to a larger size device. An estimation leads to 2200 total modules required to replace the flywheel generator EZ2. With about 400 cubic-meters the supercapacitor design would require approximately the same volume that is occupied by the EZ2.
Even though the main goals of the project have been achieved, there still are some critical points to be faced before proceeding with the building up of a full-scale converter:
- Power stage filter optimization: the designed power stage filter is a laboratory prototype. Therefore it is not optimized both in size and cost, and a proper optimization is recommended in case of scaling up of the converter;
- Losses reduction: due to the main application for which this prototype has been built, losses minimization has been not the main focus of the work. In case of usage of the proposed converter for applications where low losses are a priority, this has to be kept into account;
- Control optimization: one of the main limits of the propotype control comes from the adopted standard microcontrollers and by upgrading them the speed of the control can be significantly improved.
- Finalization of the communication and the safety system for permanent operation at full size.
- Safe power grid connection for a probably stepwise growing device.
Defining if or which other components should be upgraded will be a task that future designers should face depending on the application of the converter.
The construction of a demonstrator was possible in the laboratory at IPP. In order to further develop the concept towards 2200 modules, cooperation with industrial partners will be necessary.
Antonio Magnanimo
Doctoral thesis by Antonio Magnanimo: