First Components for the Wendelstein 7-X Fusion Device Ready
Magnet coil, plasma vessel segment and microwave heating tube for the research device at Greifswald
The goal of fusion research is to reproduce on earth the energy generation of the sun and derive energy from fusion of atomic nuclei. In order to ignite the fusion fire, the fuel in a future power plant, viz. a hydrogen plasma, has to be confined in magnetic fields and heated to temperatures of over 100 million degrees. Wendelstein 7-X – when ready, the world’s largest fusion device of the stellarator type – is aimed at investigating the suitability of this concept for a power plant. With discharges lasting up to 30 minutes it is to demonstrate the essential property of stellarators, the capability of continuous operation.
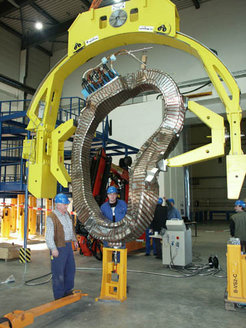
Magnet coils
IPP has taken delivery of the first of a total of 50 non-planar magnet coils – the core of the device. Their bizarre shapes are the result of sophisticated optimisation calculations; they will serve to produce a particularly stable and thermally insulating magnetic cage for the plasma. Owing to the long pulse times of 30 minutes envisaged, superconducting current leads will be used for constructing the magnets – unlike in previous devices. When cooled to low temperatures, they require hardly any energy after being switched on. A flexible superconducting cable made of niobium-titanium with an aluminium sheath was specially developed for Wendelstein 7-X. In the soft initial state it can be placed in casts and then annealed by heating. In operation the conductor is cooled with liquid helium flowing inside it to a superconducting temperature from about 4 kelvin to close to absolute zero. Two-thirds of the 60 kilometres of cable ordered has meanwhile been produced by the supplier, a consortium of European Advanced Superconductors and Europa Metalli Superconductors S. p. A.
This conductor is being processed into coils by the German-Italian consortium of Babcock Noell Nuclear and Ansaldo at ABB in Augsburg and Genoa. Three of the approx. 3.5 metres high and 2.5 metres wide coils are ready; more than half of all the coils are being processed.To conform to the rated shape within just a few millimetres the conductor windings have to be pressed into their winding form with great precision. The conductor and also the entire winding pack are electrically insulated by wrapping them with fibreglass bandages and impregnating them with epoxy resin for rigidity. Additional reinforcement is provided by solid-steel casings – manufactured as half-shells by the Swedish foundry, Österby Gjuteri AB – into which the winding packs are brazed at Babcock Noell Magnettechnik GmbH in Zeitz. Filling the space between the coil core and steel sheath with quartz sand and epoxy resin ensures uniform transmission of forces from the winding pack to the casing. Allowance has to be made for the fact that on later cooling to low temperatures the sheath, filling and winding pack contract at different rates. This is compensated for by heating the casing prior to impregnation. The expanding casing shrinks again when cooled; the temperature difference is calculated so that the coil is free of tension exactly at its low operating temperature.
The finished coil is then equipped with cooling tubes and sheeting; pedestals and holders for securing the heavy components (weighing approx. 6 tonnes) to the support structure are mounted. To check their performance all coils are then transported to a test rig at CEA in Saclay, France, and tested at low temperature. The first coil was delivered there in June 2003; two stellarator coils have meanwhile passed muster.
Planar coils
A second set of 20 planar coils is superposed on the wreath of 50 non-planar stellarator coils in order to vary the magnetic field and enhance the flexibility of the experiment. At the manufacturer’s, Tesla in the United Kingdom, 16 coils have meanwhile been wound and two have been completed. The first planar coil has also already passed its performance test at Saclay.

Plasma vessel
The first two of a total of 20 segments of the plasma vessel were delivered to Greifswald by the manufacturer, Deggendorfer Werft und Eisenbau GmbH, at the end of last year. The plasma vessel is part of the so-called cryostat, the thermally insulating vessel for both the low-temperature magnet coils and the hot fusion plasma. The approximately annular plasma chamber with a diameter of about 8 metres, which will later contain the hot plasma, serves as the inner wall of the cryostat. It is enclosed by an outer sheath 16 metres in diameter. The vacuum space between the plasma vessel and outer vessel accommodates the low-temperature coil system. A cooling plant will supply 5000 watts of helium refrigeration to cool the magnets and their support structure, i.e. a total of 425 tonnes of material, to superconduction temperature.
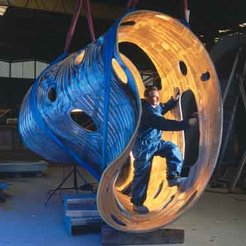
The plasma vessel placed inside the coils is matched in shape to the twisted plasma ring. The complex shape in conjunction with the high precision required – in some instances the tolerances are not greater than three millimetres – make manufacture an exacting task. The bizarre shape is reproduced in steel by assembling the ring-shaped vessel from 200 individual rings. Each ring is made up of several sheet metal strips, finger-thick and 15 centimetres wide, which are multiply creased to reproduce the curved contours. Seven such ultrahigh-vacuum-tight segments of the total 20 are meanwhile ready.
An intense water jet is then applied to cut a total of 299 apertures in the vessel segments through which the plasma will later be observed and heated. An equal number of ports, thermally well insulated and inserted between the coils, connect these apertures with the outer wall of the cryostat. As everything contracts on cooling to superconduction temperature, the ports are equipped with flexible bellows to compensate for length. Sixty ports, manufactured by the Swiss company, Romabau, are ready for dispatch and two have already been delivered.
Microwave heating for the plasma
The plasma of Wendelstein 7-X is to be heated in continuous mode by ten microwave transmitters each having one megawatt of power at a frequency of 140 gigahertz. Such transmitting tubes, so-called gyrotrons, have hitherto been built only for heating pulses of just a few seconds and powers of a few hundred kilowatts. The necessary development work and construction of the microwave heating system for Wendelstein 7-X are being done by Karlsruhe Research Centre, which coordinates the contributions made by other laboratories and industry. The prototype and first of the ten microwave generators – manufactured by the French company, Thales Electron Devices – was already successfully commissioned at Greifswald at the end of 2003. With an output power of one megawatt it is the world’s most powerful microwave transmitter running for several minutes.
It is now being used to test the transmission system, which is being developed by Institut für Plasmaforschung at Stuttgart University. The microwaves are directed into the plasma via water-cooled metal mirrors. The sophisticated components must collimate the microwaves from their ten individual beams and transmit them into the plasma at the particular location required, without destruction despite the high power of one megawatt and with the lowest possible transmission losses; they also have to be in the right polarisation state and exactly collimated. Of the 140 mirrors envisaged altogether 100 are installed. Apart from the in-vessel components, which cannot be installed till the experiment is built, the transmission system is thus complete. In the high-power tests now being conducted all components are being checked for operation in conjunction with one another – besides the transmission system, also the cooling system, high-voltage supply, measuring technique and data acquisition. In parallel, the second gyrotron, developed by the U. S. company, Communication and Power Industries, is already being built. First tests are scheduled for April 2004.
Preparing installation
Tests and preparations for installation are now in progress at Greifswald. Research and training on smaller equipment supplement the work for Wendelstein 7-X. The start of operation, scheduled for 2010, essentially depends on timely completion of components by industrial suppliers. “With complex devices such as Wendelstein 7-X industrial production and construction are in themselves already an experiment where new ground is being broken in numerous spheres”, explains Dr. Manfred Wanner, who as head of the “Basic Machine” division is in charge of component production. He further states that “the experience gained with Wendelstein 7-X will, however, also be of great benefit to the ITER international test reactor”.
Isabella Milch